Nextgen Diesel Inc.
7 Electrical Faults in Heavy-Duty Trucks and How to Address Them
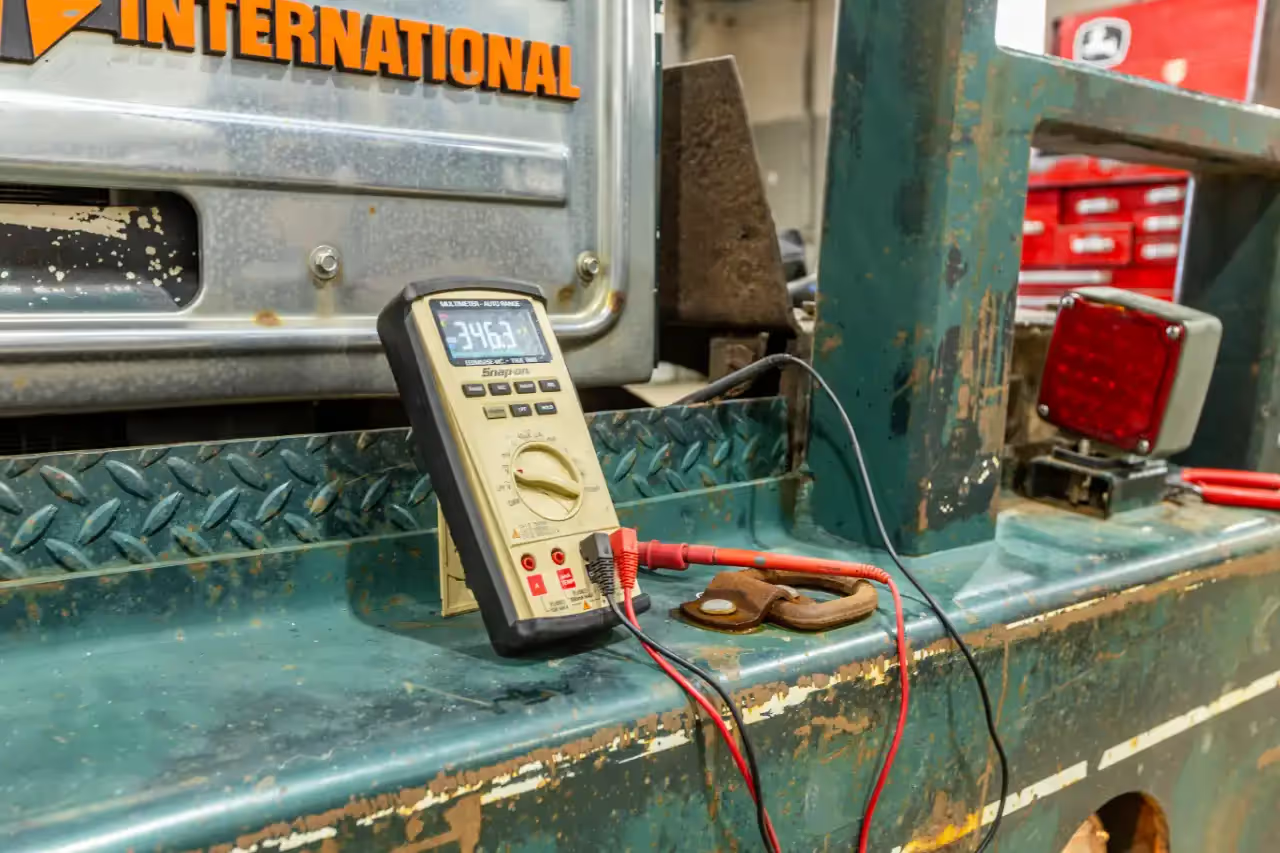
Imagine you're on a long-haul journey, miles from the nearest service station, and suddenly, your truck's electrical system fails. What a nightmare! Electrical faults can lead to unexpected breakdowns, lost time, and hefty repair bills.
Heavy-duty trucks depend on intricate electrical systems to keep everything running smoothly. So, let's dive into their most common problems and learn how to tackle them head-on, ensuring your fleet stays on the road and out of the shop.
1. Dead Batteries
Causes
Dead batteries often result from an aging battery or a parasitic draw—when some electrical component continues to use power even after the truck is turned off. Extreme weather conditions and temperatures can also wreak havoc on battery life, especially in colder climates.
Solutions
Regular battery maintenance is key. Conducting routine voltage checks can help identify a failing battery before it dies. Invest in high-quality batteries designed specifically for heavy-duty trucks, and don't forget to perform a parasitic load test to check for any parasitic draws.
2. Faulty Alternators
Causes
The alternator is responsible for keeping the battery charged and powering the electrical system when the engine is running. Over time, alternators can wear out or suffer from issues such as a broken serpentine belt or a blown fuse.
Solutions
Regular inspections of the alternator and related components can prevent breakdowns. Look for signs of wear and tear on the belt and ensure all connections are secure. If the alternator fails, qualified truck electricians must replace it.
3. Wiring Issues
Causes
Wiring problems can be the most difficult to diagnose. They can stem from corrosion, frayed wires, or poor connections. Exposure to harsh elements and vibrations can also contribute to these issues.
Solutions
Routine inspections are essential. Use a multimeter to check for continuity and ensure tight and corrosion-free connections. When dealing with wiring issues, patience and a methodical approach are crucial. Replacing corroded or damaged wires promptly can prevent bigger problems.
4. Blown Fuses
Causes
Fuses protect the electrical circuits from overloads. When a circuit draws too much current, the fuse blows to prevent damage. This can be due to a short circuit or a faulty component.
Solutions
First, consult the fuse box diagram to identify which fuse has blown. Once located, determine the root cause—whether it's a short circuit or a defective part. Replace the faulty component and install a new fuse.
5. Malfunctioning Sensors
Causes
Modern heavy-duty trucks rely on numerous sensors for optimal performance. These sensors can fail due to age, contamination, or electrical interference.
Solutions
Use a diagnostic tool to read error codes from the truck's computer. This can help pinpoint which sensor is causing the problem. Clean or replace the sensor as necessary and ensure the wiring to the sensor is intact.
6. Starter Motor Issues
Causes
The starter motor is essential for getting the engine running. Over time, it can wear out or fail due to issues like a faulty solenoid, worn brushes, or bad connections.
Solutions
Inspect the solenoid and connections first to see if the starter motor is making unusual noises or not engaging. If these are in good condition, the starter motor itself may need replacing. Regularly checking the starter system can preempt sudden failures.
7. Grounding Problems
Causes
Proper grounding is vital for any electrical system. Grounding issues can arise from loose connections, corroded ground straps, or damaged ground points.
Solutions
Inspect all ground connections regularly. Clean any corroded points and ensure all ground straps are secure. Adding additional ground straps can also improve overall system performance and reliability.
Practical Tips for Preventing Electrical Faults
- Regular Maintenance: Consistent checks and maintenance routines can catch potential issues before they become major problems.
- Quality Components: Using high-quality parts designed for heavy-duty applications can extend the life of your electrical system.
- Diagnostic Tools: Invest in reliable diagnostic tools to help identify and troubleshoot issues quickly.
- Training: Ensure your maintenance team is well-trained in handling electrical systems in heavy-duty trucks.
Conclusion
Maintaining the electrical systems of heavy-duty trucks is crucial for ensuring reliability and minimizing downtime. You can keep your fleet running smoothly by understanding common electrical faults and implementing regular maintenance routines. Remember, proactive measures are always more cost-effective than reactive repairs. Keep those diagnostic tools handy, and don't skimp on quality parts—your bottom line will thank you.
Next Gen Diesel offers professional diesel mechanics and our heavy-duty truck repair shop in Denver, North Carolina. We provide service for light to heavy-duty diesel vehicles, trailers, heavy equipment, & commercial fleets, both in-shop, & via a 30-mile mobile service radius that includes service to Charlotte, Gastonia, Kannapolis, Mooresville, Hickory, Statesville, & more.